Productie
Wat is MRP of Material Requirements Planning?
Voor productiebedrijven is een soepele levering aan eindklanten van cruciaal belang. Binnen de maakindustrie heerst er dan ook een harde concurrentie als het gaat om leverbetrouwbaarheid. Als een van de schakels in jouw productieproces hapert, kan je niet op tijd aan de verwachte vraag voldoen. Gevolg? Jouw klant klopt zonder aarzeling bij jouw concurrent aan. Een tijdige levering van producten begint bij de bron: een correct ingeschatte voorraad van materialen en grondstoffen. Hierbij is Material Requirements Planning de sleutel. Exact vertelt je graag meer over wat MRP inhoudt en wat het voor jouw productie kan betekenen.
Wat betekent MRP?
Material Requirements Planning versus Manufacturing Resource Planning
De Engelse afkorting MRP kan mogelijk voor enige verwarring zorgen. Deze wordt namelijk gebruikt voor de aanduiding van twee termen die nauw met elkaar verbonden zijn.
Material Requirements Planning
Deze term wordt ook als MRP 1 aangeduid en richt zich hoofdzakelijk op het zo goed mogelijk plannen van de inkoop- en verkoopprocessen, zodat er geen tekorten of overschotten aan grondstoffen en materialen zijn. MRP l helpt om op tijd aan de vraag te voldoen.
Manufacturing Resource Planning
In tegenstelling tot MRP 1, ligt bij Manufacturing Resource Planning of MRP 2 de focus op het plannen van het gehele productieproces. Hier gaat het dus niet alleen om materialen, maar ook om een efficiënte planning van twee andere belangrijke resources, namelijk je werknemers en machines. In feite vormt MRP 1 dus een onderdeel van MRP 2.
Waarom is een MRP belangrijk?
Hoe werkt Material Requirements Planning?
Een MRP-planning is gebaseerd op alle inkomende en alle uitgaande materialen/grondstoffen. Bovendien houdt een efficiënte MRP rekening met:
- de bestaande voorraad: de nog aanwezige hoeveelheid wordt afgetrokken van de vereiste aantallen
- een minimale bestelhoeveelheid die door de leverancier is bepaald om de kostprijs te drukken
- een veiligheidsvoorraad of minimumvoorraad om aan een onverwachte vraag te kunnen voldoen
- de besteldoorlooptijd
- de productiedoorlooptijd
Daarnaast kan de productie op twee manieren worden aangestuurd: op basis van de voorraad of orders.
Voorraadgestuurde MRP
Ordergestuurde MRP
In dit geval wordt de productie afgestemd op de inkomende verkooporders.
In de realiteit komt een combinatie van beide soorten MRP-systemen vaak voor. Een deel van het aanbod wordt daarbij gestuurd vanuit verkoopprognoses en een ander deel vanuit verkooporders.
Hoe werkt MRP in software van Exact?
Het spreekt voor zich dat jouw productiebedrijf moet kunnen terugvallen op betrouwbare software zodat iedere betrokken medewerker op elk moment over correcte cijfers beschikt.
Specifieke MRP-software berekent voor jou de hoeveelheid materialen die je nodig hebt (wat en wanneer) en de daaraan gekoppelde werkorders. Hieronder maken we dit concreet met een eenvoudig voorbeeld.
Voorbeeld van berekening van de materiaalbehoefte
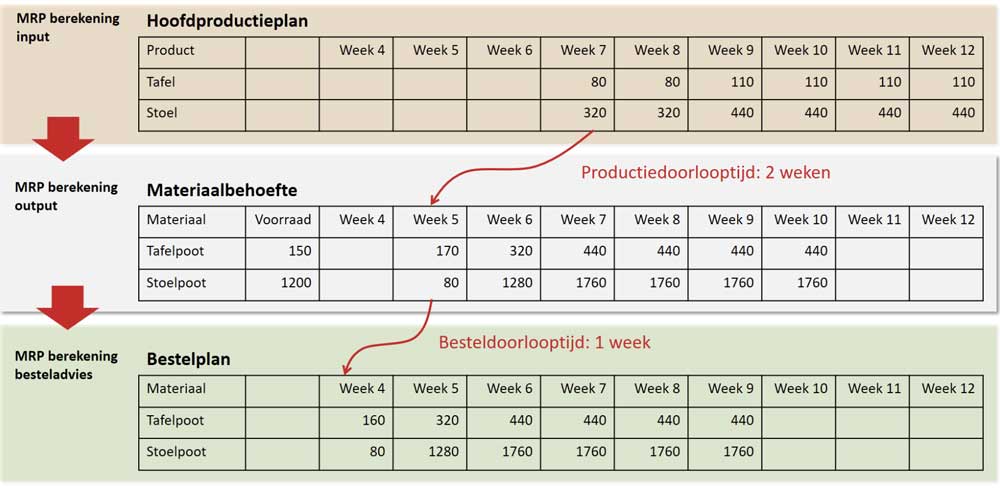
Voorbeeld van berekening van de werkorderbehoefte
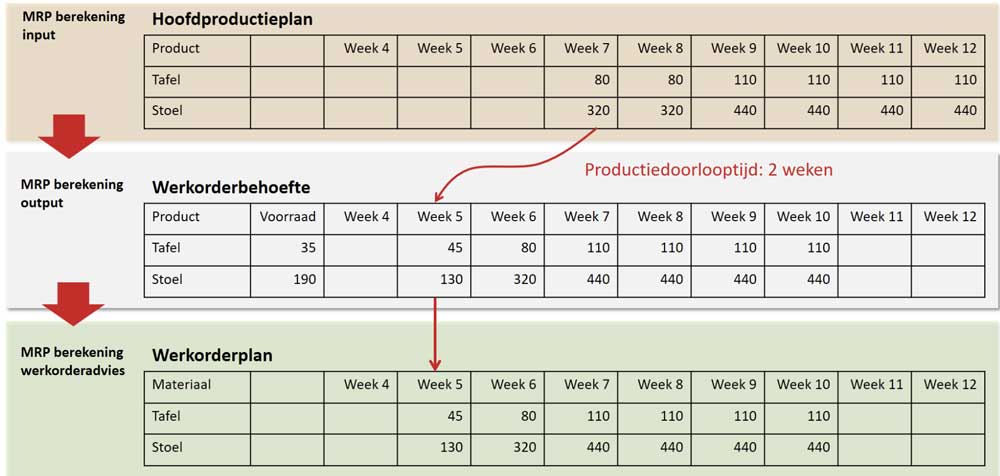
Wil je nog meer details en concrete voorbeelden zien hoe dit in de software van Exact werkt? Lees dan zeker het artikel ‘Hoe werkt MRP in Exact Online?’
De MRP-software geeft je dus advies over je bestel- en werkorders, met het voordeel dat je deze aantallen nog altijd kan aanpassen als er intussen iets in het hoofdproductieplan verandert.
Een MRP-systeem ondersteunt jouw bedrijf om de productie kostenefficiënter te maken.
Wil je meer weten over de voordelen van een MRP systeem voor jouw bedrijf?