Blog
Moving away from single use products, manufacturers gain value from disassembly in the circular economy
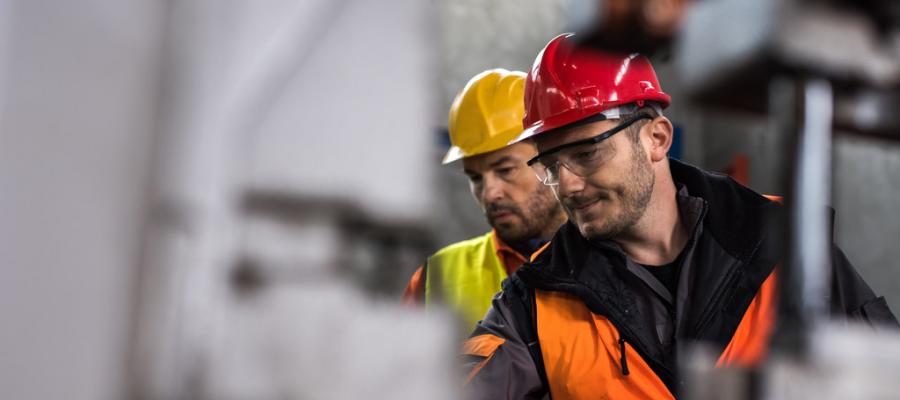
In today’s circular economy buyers expect that manufacturers take ownership of the full product lifecycle. They expect that their suppliers assume responsibility at the end of a product’s lifecycle and take products back when they are no longer in use. Manufacturers increasingly address this need and increasingly move away from manufacturing throw-away, single use products to more sustainable and repairable products.
Taking used products back
The need to take-back products can be driven by the need to comply with waste laws. These laws may dictate that suppliers take back certain products (such as e-waste, batteries) and take care of the disposal process.
Firms may also want to pro-actively take used products back as part of their strategy to strengthen customer relationships. For example, manufacturers may offer ‘lifetime warranties’ or ‘trade-in services’. Customers may return their products in case of warranty issues or when they want to trade-in used products for a credit towards their next purchase.
Manufacturers may want to improve sustainability by providing their customers with an option to lease or rent the product instead of purchasing it. Such ‘product-as-a-service’ (PaaS) business models keep ownership with the manufacturer (or service provider), who remains responsible for the product throughout its entire life cycle. The manufacturer adds value through ongoing services (e.g. repair, maintenance, etc.). At a certain moment, the customer decides the product is no longer needed and the product is then returned to the original manufacturer. The manufacturer remains responsible for handling product returns and keeping the product ‘in circulation’ for as long as possible, for example by taking used products back and re-market them as refurbished products. If manufacturers are able to extend a product’s lifecycle by using a PaaS strategy, they’ll contribute towards improving sustainability1.
Disassembly helps manufacturers to retain product value
Disassembly of end-of-life products does not only contribute towards sustainability goals, but it can also be very attractive from a business point-of-view. The ability to fully (or partially) disassemble a product after being used helps to retain the value of its parts and subassemblies. These ‘harvested’ parts can then be sold, reused, reassembled, or recycled. It can be worthwhile to extract valuable materials (such as precious metals). The recent rise in shipping costs and increase in delivery times due to Covid, make it even more attractive to disassemble and reuse products.
Disassembly challenges
It can be challenging to take products back and disassemble them. For example, customers do not have an incentive to return products or it can be costly to organize reverse logistics in case products are spread all over the world. Product characteristics can be challenging as well. Most products are not designed with ease of disassembly in mind. Products may contain many different parts and different materials. Products may even contain inseparable subassemblies caused by irreversible operations during the original manufacturing process. Such irreversible operations make it impossible to disassemble parts and return them to their original state. There is also risk of damaging materials when disassembling. Often it is also necessary to spent time on quality control activities such as cleaning, testing, or performing material assessments. Overall, it can be time consuming (and thus costly) to remove valuable parts and subassemblies. The commitment to take products back after being used thus creates a challenge for manufacturers on how to maximize the value of returned products. In order to address these challenges many firms design products with a focus on disassembly and repairability. Best practices include Gerrard Street (headphones) or Fairphone (mobile phones).
Disassembly in Exact Online
Exact Online for Manufacturing helps you to efficiently manage the disassembly process, and at the same time it helps you to gain insight into the cost of disassembly operations such cleaning, inspection, and quality control.
We’ll use the Bill of Materials (BOM) to manage the disassembly process. In Exact Online, a BOM typically contains the materials and operations needed to produce or assemble products. You can also use this BOM to manage the disassembly of a product. You can plan and track time spent on disassembly work (such as cleaning, inspection, etc) and monitor the cost and planned output of the disassembly work. The output can contain products fit for reuse, but it can also contain waste, or parts that did not pass quality inspection.
Step 1: create a virtual disassembly item with a BOM
We’ll use a ‘virtual’ item to manage the disassembly process. It is a virtual item since we do not physically stock this item, we merely use it to manage the disassembly process. This item has a linked Bill of Materials (BOM) that contains the routing of disassembly operations, materials needed, and the planned output of the disassembly work. The planned output is registered using by-products.
Routing of disassembly operations in a BOM
In this example we’ll use 4 operations: cleaning, disassembly, repairs, and quality control. We’ll estimate that each activity takes 6 minutes per item. These operations are included in the BOM (see image below).
Materials needed in a BOM
Here we specify the item to be disassembled. Used products can be put on stock and once sufficient stock is built up we can work on the disassembly. The image below shows the item to be disassembled included in the material list of this BOM.
The planned output of the disassembly work
We’ll use by-products to track disassembled items. Typically, by-products are generated during the manufacturing process (e.g. scrap, damaged products), but we can also use them to manage the output of the disassembly work. The image below shows the materials of the original product (left) and the output of the disassembly (right). In this case the desired output is 3 metal parts (A,B,C) and an inseparable subassembly. Given that there is a risk that parts may damage during the disassembly process we’ll also include the option to receive any of these parts that did not pass quality inspection.
Step 2: Issue a workorder for disassembly
After setting up the BOM we can start by creating a work order for disassembly. In this case we want to disassemble 3 products.
Step 3: Disassembly
Next, we’re start with the disassembly work. You can track time spent in Exact Online. In this case we spent nearly 2 hours on disassembly work, mainly caused by some additional repair work. Tracking time spent gives insight into the cost of disassembly.
Step 4: Receive disassembled products as by-products
We can register the output of the disassembly work and put disassembled items on stock. In this case we received both damaged and non-damaged parts. Please note that in this case we only use one stock location. Of course, you can work with various stock locations, helping you to separate damaged from non-damaged parts.
Step 5: Gain insight into the disassembly cost
After disassembly, we can complete the work order. We can gain valuable insights into the cost of disassembly. For example, we can monitor planned vs. actual disassembly costs, as shown in the figure below.